3D tisk nachází uplatnění v železničním průmyslu
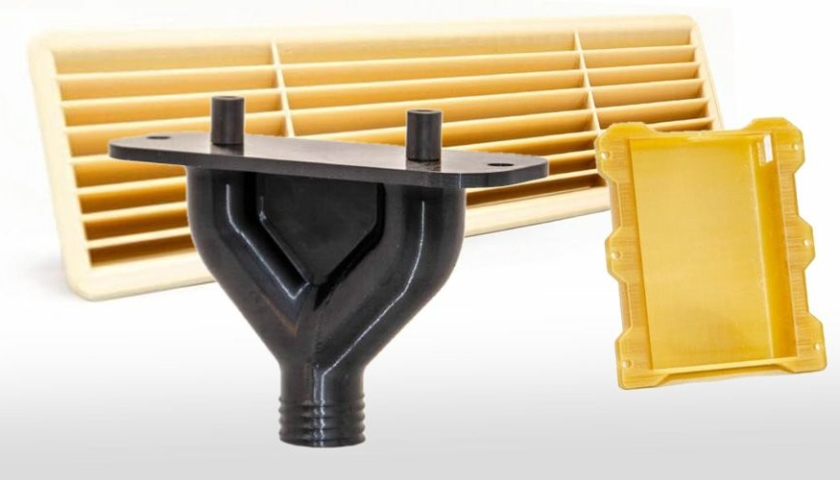
Aditivní výroba se osvědčuje při výrobě náhradních dílů. Platí to i při opravách kolejových vozidel, kde 3D vytištěné díly nahrazují obtížně sehnatelné originální komponenty.
Inzerce
Délka životního cyklu může u vlaků dosahovat až 30 let, což je velkou výzvou z pohledu náhradních dílů. Některé náhradní díly se také v čase vyvíjejí, což bývá oříšek pro tradiční výrobní metody. Zatímco díly pro novější vlaky jsou většinou široce dostupné, u vlaků starších 15 let je situace složitější. Ve většině případů již takové náhradní díly nejsou k dispozici, nebo pro ně neexistují formy a další výrobní nástroje. Náklady na individuální výrobu takových součástí jsou velmi vysoké a ekonomicky nevýhodné pro všechny zúčastněné strany.
3D tisk přináší možnost vyrábět náhradní díly jednotlivě nebo v malých sériích. Je také efektivnější co do nákladů a díl můžete vyrobit přímo v místě potřeby. Tradiční výrobní metody, například frézování a vstřikování, jsou dražší – zčásti kvůli množství materiálu, který se během procesu vyplýtvá, zčásti kvůli potřebě vyrábět najednou větší série, aby bylo dosaženo nákladové efektivity.
Nasazení 3D tisku umožňuje zamezit plýtvání materiálem. Není také nutné skladovat velké množství náhradních dílů. Nemusíte ani čekat, až budou součásti (uskladněné na vzdálených místech) dopraveny tam, kde je jich potřeba. Náhradní díly se vytisknou tam, kde je jich potřeba, a tehdy, kdy jsou potřeba. Při efektivně vynaložených nákladech lze rozvíjet a rozšiřovat výrobní síť. Podle odhadů to může urychlit výrobu náhradních dílů až o 90 % ve srovnání s tradičními metodami.
Železniční standardizace
I u nejjednodušších součástí záleží na materiálu, ze kterého jsou vyrobeny. Všechny materiály používané v železničních vozidlech musí splňovat normu EN45545-2. To proto, aby bylo dosaženo nejvyšší možné úrovně bezpečnosti v případě požáru. Existuje široká škála materiálů, které tuto normu splňují. Různé materiály mají různou klasifikaci, optimální materiál se tedy vybírá podle požadavků dané aplikace.
MiniFactory Ultra – ideální 3D tiskárna pro železnici
Finský výrobce MiniFactory spolupracuje s výrobci materiálů i dodavateli dílů při hledání materiálů vhodných pro různé aplikace – a dokonce na optimalizaci výrobních postupů pro konkrétní materiály. Řešení MiniFactory Ultra přináší vše potřebné pro 3D tisk nejnáročnějších a nejodolnějších polymerů pro výrobu v oblasti kolejových vozidel.
3D tiskárna MiniFactory Ultra umí bez kompromisů vyrábět z více různých materiálů s certifikací podle EN45545-2 – od tiskových strun na bázi PA a PC až po vysoce výkonné materiály jako ULTEM 9085 nebo PEKK. Vyhřívaná komora tiskárny s teplotou 250 ˚C zajišťuje optimální a konzistentní prostředí pro výrobu dílů. Servopohon zařízení posouvá opakovatelnost a spolehlivost výrobní technologie na zcela novou úroveň. Bez ohledu na zvolený materiál tak bude tato 3D tiskárna připravovat výtisky vždy ve stejně vysoké kvalitě a se stejnou opakovatelností.
Software Aarni pro sledování postupu aditivní výroby byl vyvinut přímo pro 3D tiskárnu MiniFactory Ultra. Lze jej využít při kontrole kvality a certifikaci procesu výroby náhradních dílů. Jakmile je náhradní díl otestován a schválen k použití výrobcem, lze Aarni využít při kontrole kvality. Zajistí, aby byly i další náhradní díly tisknuty výrobcem schváleným postupem. Jednotnost takového postupu je klíčová z hlediska spolehlivosti výroby dílů a jde o významný faktor právě při přípravě náhradních dílů v železničním průmyslu.
V aplikaci Aarni lze vizuálně zobrazit klíčové parametry dílu. Pro každý výtisk také můžete získat samostatný výrobní protokol. Aarni je tak velmi praktickým pomocníkem při certifikaci dílů.
Tato součást ventilace má optimalizované proudění vzduchu a upevnění pomocí zacvaknutí. Výroba tohoto dílu je velmi náročná a vzniká při ní obvykle velké množství odpadu. Aditivní výroba zde výrazně snižuje náklady: Velikost dílu je 320 × 100 × 30 mm a náklady na jeden díl z materiálu ULTEM AM9085F jsou 55 €
Tento držák snímače je lehký, spojuje vše v jednom dílu, včetně krytu kabeláže a upevňovacího závitu. Má složitou geometrii, kterou nelze vyrobit tradičními výrobními metodami bez použití složitějších forem. Velikost dílu je 160 × 110 × 60 mm a jeden kus vyjde na 25 € při 3D tisku z materiálu ULTEM AM9085F
Kryt baterie vytisknutý z materiálu PEKK. Jde o materiál splňující normu EN45545-2 s mimořádně dobrými chemickými a mechanickými vlastnostmi, což z něj činí vhodnou volbu pro danou aplikaci. Tento kryt by bylo snadné vyrobit tradičními metodami. Při aditivní výrobě však nedochází k plýtvání materiálem, takže náklady na jeden díl jsou výrazně nižší. Velikost dílu je 120 × 100 × 30 mm a náklady na jeden kus vyrobený z PEKK-A činí 90 €
Zdroj: 3Dwiser, MiniFactory
Další článek: V největším závodě na zpracování dřeva na severní polokouli instalují turbínu z Plzně