Hybridní výroba spojuje 3D tisk s přesným obráběním
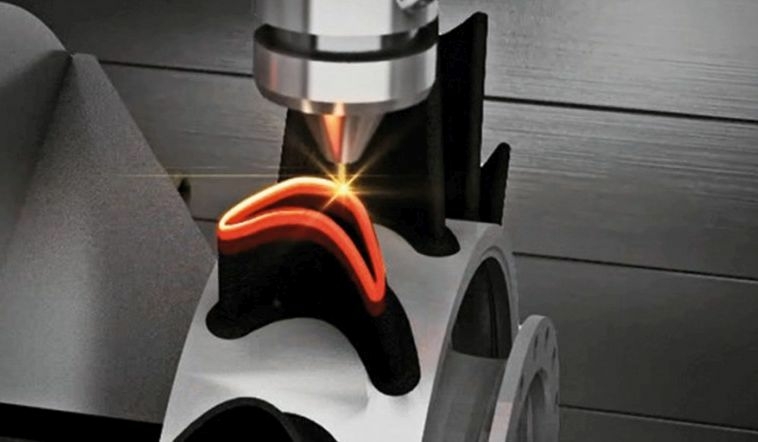
Výroba kovového dílu nejčastěji vychází z odebírání materiálu obráběním. Aditivní technologie nám ukázaly, že to jde i naopak. Pojem hybridní výroba pak kombinuje to nejlepší z obou těchto světů.
Inzerce
Aditivní a substraktivní výrobní metody, respektive 3D tisk a obrábění, jsou běžně chápány jako vzájemné protipóly, kdy každá technologie slouží svému vlastnímu účelu, jemuž nevyhovuje technologie opačná. V hybridních strojích se tyto metodiky potkávají a obohacují výrobní proces o propojení vzájemných výhod.
Obecně platí, že aditivní technologie má největší smysl ve výrobě tvarově velmi složitých komponent anebo dílů vybavených vnitřními dutinami či odlehčenými mřížkovými strukturami. Využívá nadstandardní volnosti, která jí je umožněna schopností vyrábět i velmi nekonvenční tvary. Proti tomu konvenční CNC obrábění je vysoce produktivní u standardních dílů a navíc narozdíl od 3D tisku poskytuje vysokou výrobní přesnost a dodržení i velmi náročných rozměrových tolerancí.
To nejlepší z obou metod
Hybridním postupem lze vyrábět díly složitých tvarů i s vnitřními dutinami, přičemž dodržení nutné rozměrové a tvarové přesnosti zajistí obrábění, jež může být aplikováno průběžně během stavby výrobku v jednotlivých vrstvách. Proces konstruování a následné výroby dílu vyžaduje respektování zásad obou prolínajících se metodik – jedině tak lze jejich potenciálu využít na maximum. S tím se pojí orientace vyráběného dílu ve výrobním prostoru, v níž je potřeba zohlednit samotnou vyrobitelnost z hlediska konkrétních tvarů takového dílu. Sekvence střídavého nanášení a odebírání materiálu musí mít logiku a zároveň je potřeba zabránit možným kolizím nástroje s výrobkem stejně jako je tomu v případě konvenčního CNC obrábění.
DMG MORI
Jako první z velkých výrobců se již v roce 2013 do hybridní výroby naplno ponořila DMG MORI, která na veletrhu Euromold představila stroj Lasertec 65 3D, vyvinutý v německém závodu Sauer. Zařízení vycházející z pětiosého obráběcího centra DMU 65 monoBlock nabídlo unikátní schopnost vyrobit z práškového kovu pevný díl a ten následně obrobit do požadovaných nejmenších detailů.
Oproti průmyslovým 3D tiskárnám na tisk kovů jeho výhoda spočívá nejen v následném obrobení výrobku, ale také v rychlosti a impozantním objemu. Lasertec 65 3D dokáže zpracovat 3,5 kilogramu materiálu za hodinu, takže je až dvacetinásobně rychlejší než zavedená aditivní výroba. Vytvořit v něm navíc můžete produkt o průměru až 650 mm a výšce 360 mm s maximální hmotností do jedné tuny. Podobnou aditivní technologii v kombinaci s obráběním najdeme i ve stroji DMG Mori Lasertec 4300 3D. V tomto případě jde o první soustružnicko-frézovací centrum vybavené technologií laserového navařování kovového prášku. Zpracovat v něm můžete výrobky o rozměru až 660 × 1500 mm a hmotnosti do 1,5 tuny.
Mazak
V roce 2014 na veletrhu JIMTOF v Japonsku představil svoje řešení pro hybridní výrobu Mazak. Víceúčelový stroj Integrex i-400 AM, který firma vyvinula ve spolupráci s mladou společností Hybrid Manufacturing Technologies, kombinuje dva typy laserového nanášení kovu (pro rychlou nebo velmi přesnou výrobu) a pětiosé třískové obrábění. V současnosti nabízí Mazak již tři různé stroje, které se liší stupněm svojí výbavy – kromě výše uvedeného ještě jednodušší typ i200S AM a dále stroj Variaxis j-600 AM, který aditivní výrobu doplňuje o navařování elektrickým obloukem.
Trumpf
Mnohaleté zkušenosti s hybridní výrobou má německý Trumpf. Oproti svým konkurentům má velkou výhodu spočívající v bohatém know-how v oblasti vývoje laserové techniky. S principem označovaným jako LMD (laser metal deposition) pracuje již sedmnáct let, přičemž v poslední době dosáhl značných pokroků také v metodě LMF (laser metal fusion), kterou je vybavena jeho průmyslová 3D tiskárna TruPrint 1000, představená na veletrhu Formnext 2015.
Hybridní výrobu u Trumpfu zastupují vyspělé stroje TruLaser Cell 3000 a TruLaser Cell 7040. Tyto prostřednictvím laserového navařování dokážou doplnit existující díly o další prvky tak, že nejprve nataví existující kov, načež do tohoto místa nanášejí kovový prášek. Rychlost výroby tímto způsobem dosahuje 500 centimetrů krychlových za hodinu.
Matsuura
Hybridní obráběcí stroj nabízí také japonská Matsuura, jejíž Lumex Avance 25 zvládá klasické laserové sintrování kovového prášku kombinované s frézováním. Zajímavé je, že frézování probíhá nikoliv až po „vytištění“ hrubého výrobku, nýbrž po každých deseti vrstvách aditivně naneseného kovu o celkové tloušťce 0,5 milimetru. Matsuura tím pádem dokáže obrobit i „vnitřní“ části dílů předtím, než je aditivní postup nadobro pro další zásahy znepřístupní. Efektivně se proto tento postup používá například pro výrobu forem vybavených kanálky pro tzv. konformní chlazení.
Kovosvit MAS
Originální patentovanou technologií aditivní výroby disponuje také česká společnost Kovosvit MAS, která svůj stroj Weldprint MCV 5X vyvinula ve spolupráci s ČVUT. Ve své výrobní komoře využívá navařování elektrickým obloukem technologií MIG/MAG v kombinaci s pětiosým obráběním. Od zahraniční konkurence se chce český výrobce odlišit unikátním řešením řetězení výrobních operací, zahrnující také čištění svarů, odsávání nečistot a chlazení výrobku. Pracovní prostor je monitorován termokamerami, které sledují procesní parametry v reálném čase, díky čemuž lze zaručit kvalitu dílců a po validaci stroje je certifikovat. Obchodní příležitosti vidí Kovosvit MAS zejména v oblasti oprav rozměrných kovových dílů.
Siemens
Na rozvoj hybridních výrobních technologií musejí reagovat také výrobci CAD/CAM softwaru. Iniciativu projevuje například Siemens, jenž do svého konstrukčního systému NX postupně zavádí nové nástroje specializované právě na aditivní i hybridní výrobní postupy, berouc v potaz také související oblast topologické optimalizace.
Další článek: Renishaw na MSV 2017 představí nový stroj na 3D tisk kovů