O koupi jeřábů Demag a Konecranes rozhodla výroba v ČR a rychlý servis
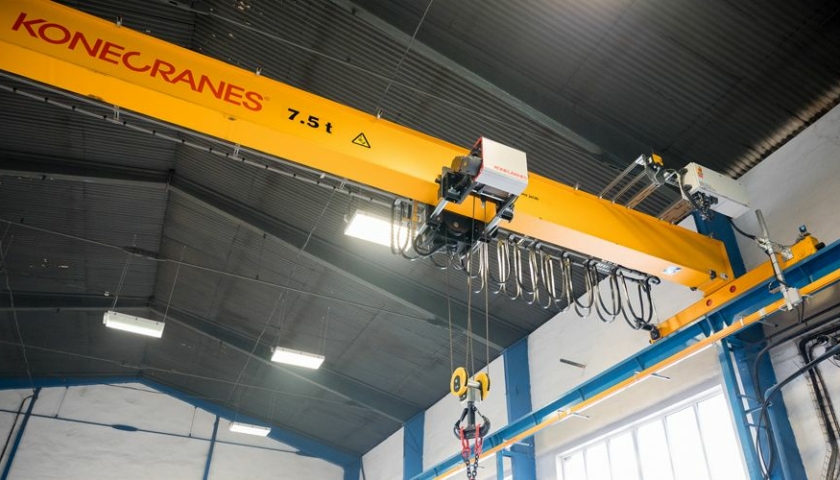
Dva jeřáby Demag a tři jeřáby Konecranes pracují v severomoravské firmě Therma FM. Podílejí se zde na výrobě toroidních jader pro výrobu transformátorů a tlumivek. Tento výrobce, který letos oslaví 24 let od svého vzniku, patří k významným evropským hráčům. O rozhovor jsme požádali jednoho z jednatelů, pana inženýra Miroslava Křivu.
Inzerce
Na úvod našim čtenářům prosím představte společnost Therma FM. Čím se zabývá, jakou má historii, kde sídlí?
Therma FM je rodinná firma založená v roce 1998. Sídlo i výrobu máme v obci Pržno, v okresu Frýdek-Místek a zaměstnáváme přes 100 pracovníků. Naším hlavním produktem jsou magnetické obvody pro transformátory a tlumivky. Tyto obvody, označované také jako toroidní jádra, se vyrábí z elektrotechnické oceli.

Pro některé čtenáře může být pojem elektrotechnická ocel neznámý, přibližte nám vlastnosti tohoto materiálu.
Elektrotechnická ocel je ocel s vyšším obsahem křemíku, podle specifických elektromagnetických vlastností se dále dělí na orientovanou a neorientovanou. Orientovaná je využívána pro výrobu magnetických obvodů, které tvoří základní díl transformátorů a tlumivek. Neorientovaný elektrotechnický pás nachází využití při výrobě elektromotorů. Pásová elektrotechnická ocel je naším hlavním vstupním materiálem, kupujeme a dovážíme ji v různých šířkách a jakostech doslova z celého světa od Německa, přes USA, Jižní Koreu až po Japonsko. Nejlepší transformátorová ocel má nízké wattové ztráty a vysokou indukci.
Jak vypadá vlastní proces výroby?
Materiál v požadované šířce se navíjí na trn. Trny jsou kruhové, čtvercové nebo oválné. Kruhové se stáhnou z trnu a drží tvar, pak následuje žíhání v pecích. Ostatní tvary se musí žíhat ještě na trnech, jinak by se zbortily. Žíháním na cca 800 stupňů se obnoví elektromagnetické parametry, degradované pnutím, které se do materiálu vneslo během ohýbání. Tím jsou některé typy magnetických obvodů hotové. U jiných ještě následuje lepení ve vakuovací stanici, sušení a následně se rozřezávají na polovinu, kvůli snazší montáži na místě určení. Rozřezáním se opět vnáší další pnutí a zhoršují se vlastnosti, ale celým předchozím postupem se snažme ztráty minimalizovat. Úspora práce při montáži je pak pro zákazníky natolik důležitá, že tato půlená C jádra jsou velmi oblíbená.

Kam všude výrobky dodáváte?
Zákazníky máme především v Evropě: v Polsku, Německu, Maďarsku, Itálii či Francii, v Česku zůstává asi 40 % produkce.
Jakou máte pozici ve svém oboru?
Zpracujeme 200 tun měsíčně, z toho je 180 tun magnetických obvodů, zbytek jsou jiné výrobky. Škála produktů, i když to na první pohled tak nevypadá, je nesmírně široká. Snažíme se být konkurenční nejen kvalitou, ale i rychlostí dodávek, což je pro zákazníky často klíčový parametr, proč si objednat výrobky u nás. Také máme 100% kontrolu kvality, každý náš výrobek musí mít změřené parametry a vystavený certifikát.

Při množství materiálu, který denně zpracováváte, musíte mít dobře vyřešenou logistiku.
Samozřejmě, manipulujeme především se svitky ocelových pásků a používáme k tomu mostové jeřáby Demag a Konecranes a vysokozdvižné vozíky. Maximální hmotnost, kterou v současnosti potřebujeme manipulovat, je 5 tun. Ale do budoucna se připravujeme na větší a těžší svitky.
Co vás vedlo k volbě jeřábů Demag a Konecranes? Kolik jeřábů s jakými nosnostmi využíváte?
Máme celkem 5 mostových jeřábů od Demag a Konecranes, které jsme instalovali do našich hal v letech 2017 až 2021, nosnost se pohybuje od 1 t do 7,5 t. Původně jsme areál koupili včetně jeřábů, a ty nyní postupně obnovujeme. Některé jsme posunuli do krajní polohy a slouží nám jako záložní. Ale jiné jsme museli odstranit, protože už nebyly vyhovující. Jeřáby, které jsme tu měli v minulosti, byly značně předimenzované. Oproti nim jsou ty nové mnohem pohotovější a rychlejší, vybavené mikropojezdy, které umožňují pohybovat s břemenem velmi citlivě. Oceňujeme také aktivní stabilizaci proti rozkývání. Prostě na nich vidíte, že jsou na úrovni doby a velice rychle jsme si na ně zvykli.

Hledali jste standardní řešení, nebo jste měli speciální požadavky na vybavení jeřábů?
Jde o standartní provedení jeřábů. Máme tu značky Demag a Konecranes, které mají ale obě jednoho majitele, rozdíl mezi nimi je vidět například v konstrukci kočky. Také si každá značka vyvíjí vlastní řídicí systém. Všechny jeřábové nosníky se vyrábí v České republice ve Slaném. Původně jsme koupili dva jeřáby Demag a po akvizici Demagu firmou Konecranes jsme pro další tři jeřáby volili ekonomičtější variantu v podobě jeřábů značky Konecranes. Za sebe mezi nimi nevnímám velký rozdíl, pro mě je podstatné, že se vyrábí v České republice a zastřešuje je jedna firma.
Jak svoje rozhodnutí hodnotíte s odstupem? Jste spokojeni se svou volbou?
S jeřáby jsme spokojeni, hledali jsme seriózního dodavatele s dobrými referencemi a vybrali jsme si dobře.
Co na jeřáby Demag a Konecranes říkají vaši zaměstnanci, kteří s jeřáby denně pracují?
Ti oceňují především rádiové ovládání, díky němu jsou přímo v místě manipulace a mají plnou kontrolu nad tím, kam materiál ukládají.
Změna, na kterou si pořád ještě zvykají, je limitovaná nosnost. Nové jeřáby kontrolují pomocí čidel hmotnost břemene, pokud přesáhne 110 % nosnosti, neumožní s ním manipulovat. Já jsem ale rád, jeřáby ani jeřábové dráhy se díky této ochraně neničí a prodlužuje se jejich životnost.
S jeřáby pracujeme v podstatě neustále, takže nejvíce se opotřebovávají ovladače, občas je nutné vyměnit spínač. Důležité ale je, že rádiová komunikace s jeřábem funguje bezvadně.
Bavíme se tu ve velmi racionální a technické rovině, ale odborníci tvrdí, že každá volba je také emocionální záležitost. Jaké emoce cítíte v souvislosti s vašimi jeřáby?
Každý vědomě či podvědomě hodnotí své obchodní partnery, a to i podle strojního vybavení. Takže mě těší, že když k nám přijedou zákazníci nebo auditoři, vidí zde jeřáby nejlepších značek, i to je naše vizitka.
Jak byly domluvené termíny dodání jeřábů a jak se je podařilo splnit?
Termíny dodání se pohybují mezi 12–16 týdny po podepsání kontraktu a ve všech případech byly dodrženy, jak jsme se domluvili.

Mluvil jste o připravované změně, která si bude žádat manipulaci s vyššími hmotnostmi. Co máte v plánu?
K tomu vám musím říci něco o dělicí lince na pásový materiál. Abychom dokázali rychle reagovat na poptávku, pořídili jsme si před časem podélně dělicí linku, na které můžeme širokou pásku rozdělit na užší pásky, podle toho, jakou šířku toroidního jádra zákazník potřebuje. Tento dělicí agregát nám dává velkou výhodu. Nemusíme mít všechny šířky skladem ve velkém množství.
Poslední koupený jeřáb má nosnost 7,5 tuny, to je dostačující pro svitky se vstupní šířkou 420 mm, které aktuálně dokážeme zpracovat.
Dnes ale už stavíme novou dělicí linku, která zvládne vstupní šířku pásu 1 250 mm, což je maximum pro elektrotechnickou ocel. Spuštěna by měla být v polovině roku 2022. Na tomto stroji budeme pro sebe i zakázkově dělit jakýkoliv materiál v tloušťkách 0,2 až 0,8 mm, to znamená i hlubokotažné oceli nebo barevné kovy, hliník a podobně. A právě do tohoto provozu potřebujeme jeřáb s vyšší nosností, nyní máme 7,5 tun, ale další bude 10tunový.
Investujete i v době určité ekonomické nejistoty, co od toho očekáváte?
Staneme se firmou, která dokáže dělit pásy z celého světa, od jakéhokoliv výrobce elektrotechnické oceli. Materiál si budeme sami upravovat na potřebnou šířku, a budeme jej mít k dispozici okamžitě. Všude vidíme tlak na úspory elektrické energie a celý transformátorový průmysl se snaží, aby vstupní materiál měl co největší indukci a co nejmenší ztráty. Dříve hledisko ztrát hrálo roli jen u opravdu velkých transformátorů, ale požadavky na úspory už cítíme i u menších transformátorů. Nová podélně dělící linka zvýší naši konkurenceschopnost.
Jeřáb s velkou nosností a zpevnění jeřábové dráhy na tomto připravovaném pracovišti je investicí do budoucnosti.
Na závěr by mě zajímalo, jak je u vás vyřešen servis jeřábů?
Firma Konecranes and Demag, s níž máme servisní smlouvu, má tady na severní Moravě zkušené profesionály. K nám jezdí velice operativně pracovníci z Ostravy, běžně tu jsou i za 3 až 4 hodiny od zavolání. Je to dáno také tím, že náš region má silné strojírenství a v okolních podnicích jsou stovky jeřábů, což nám přináší výhodu rychlého servisu a dostupnosti náhradních dílů.
Také je dobré, že máme celou flotilu jeřábů od jednoho dodavatele, pravidelné revize udělají během jedné návštěvy.