„O kvalitě nepotřebujeme mluvit, my ji vytváříme,“ říká Zoltán Gorta
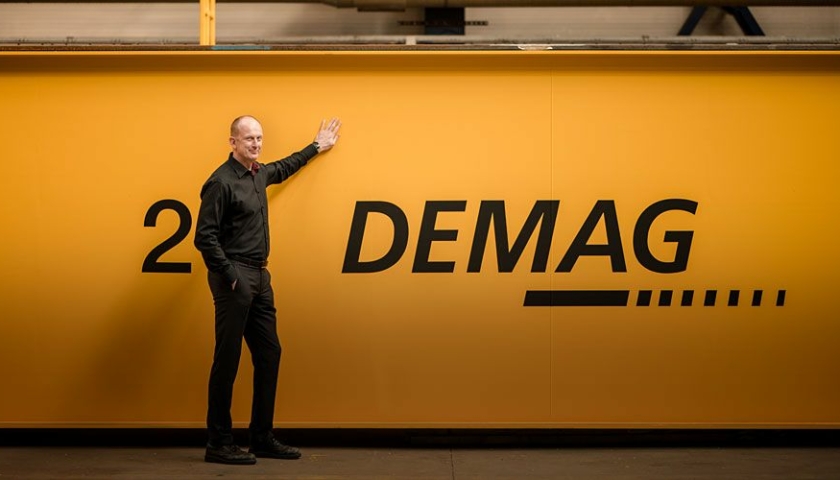
Ve středních Čechách ve městě Slaný se vyrábí špičkové jeřáby značek Demag a Konecranes. V rámci koncernu Konecranes patří tento závod k nejprogresivnějším a je znám vysokou kvalitou své produkce. Výrobními halami nás provedl a na otázky odpovídal pan Zoltán Gorta, jednatel českého zastoupení Konecranes and Demag.
Inzerce
Jaké jeřáby se zapsaly do vaší knihy rekordů?
Nejmenší jeřáb, který jsme vyrobili, měl rozpětí 2,5 metru a nosnost 1 tunu – takže takový drobeček do garáže.
Z hlediska nejvyšší nosnosti byl naším rekordem jeřáb pro ruského zákazníka s kapacitou 350 tun. Tato zakázka byla navíc unikátní v tom, že nosníky byly šroubované ze dvou kusů, aby bylo možné je rozebrat a zase smontovat.
Nejdelší zde vyrobený jeřáb byl pro německou firmu Airbus a měl rozpětí 100 metrů.
Rekordní je i produktivita našeho závodu, v některých obdobích vyrábíme až 8 jeřábů denně.
Zejména jeřáby Demag jsou považované na etalon kvality. Jak je těžké si takovou reputaci získat a dlouhodobě udržet?
Pověst značky Demag je daná už historicky, letos slaví 202 let od založení, a to už něco znamená. Demag je synonymum pro vysokou kvalitu, která vydrží. Samozřejmě po přestěhování výroby z Německa k nám do Slaného se někteří zákazníci potřebovali ujišťovat, že je všechno, jak má být. Jezdili si k nám zakázky kontrolovat a přebírat, ale získali jsme si jejich důvěru, a když přijedou dnes, tak jen na přátelskou návštěvu.
Za kvalitní výrobou si stojíme a věnujeme jí neustálé úsilí. Organizaci všech procesů máme vyřešenu tak, abychom si byli jisti, že od nás odcházejí jen dokonalé výrobky. Podobně, jako když člověk dýchá, je pro nás kvalita samozřejmou součástí naší práce. Až se nám zdá zbytečné o ní stále dokola mluvit. Máme svůj vysoký standard, který všichni naši zákazníci znají, a který si držíme.
Mluvil jste o stěhování výroby, seznamte nás prosím s historií závodu ve Slaném.
Firma byla založena v 60. letech pod názvem Agrostav. Zaměření bylo už v té době na zdvihací zařízení, v 80. letech došlo ke specializaci na průmyslovou zdvihací techniku. V devadesátých letech si nás vyhlédla německá firma Demag jako partnera pro východní Evropu. Postupné skupování podílu firmy se završilo v roce 2000, kdy se Demag stal jediným majitelem. Novodobá historie firmy se začíná psát v roce 2002, tehdy se majitelé Demagu rozhodli, že část výroby v Německu se uzavře a přesune do Slaného.
Malý závod, který obsluhoval Československo a východní Evropu se stal součástí skupiny, která je velkým hráčem na trhu. V roce 2004 už byly v provozu nové haly a od té doby obsluhujeme velké a významné zákazníky.
Výroba se sem přesouvala v několika krocích, jak to šlo postupně?
V první fázi, v roce 2004, jsme převzali výrobu takzvaných procesních jeřábů, což jsou zpravidla velké, složité, individuálně navržené jeřáby. Vyráběli jsme jich přibližně 50 až 70 ročně. Později, v roce 2015, jsme se opět rozrostli, tentokrát o výrobu standardních jeřábů, které jsou relativně jednoduché a zákazník si je nakonfiguruje podle katalogu, podobně jako automobil.
Vaše firma se jmenuje Konecranes and Demag a obě tyto značky zde vyrábíte, jak se v tom vyznat?
Demag je vnímaný jako lídr z hlediska kvality, jsou to jeřáby, které při standardní servisní péči spolehlivě fungují desítky let. Konecranes je mladší firma, takový žralok, který se dostal na trh a našel si svoji cestu, jak oslovit zákazníky. Obě tyto značky mají stejného vlastníka a na trhu se velmi dobře doplňují.
V České republice jsou zastřešeny firmou Konecranes and Demag s. r. o. Jakou značku zákazníkovi nabídne náš obchodník závisí od cenové hladiny, kterou je uživatel ochoten investovat. V jisté malé míře si obě značky konkurují. Vše záleží na komunikaci mezi zákazníkem a našimi obchodníky, kteří dokáží navrhnout nejlepší řešení podle individuálních potřeb.
Vraťme se zpátky do výroby. Kolik jeřábů ročně dokážete dodat zákazníkům?
Jak už jsme si řekli, vyrábíme zde dvě velmi odlišné skupiny produktů. Procesní jeřáby jsou komplikované a jejich produkce se drží mezi 20 a 35 kusy ročně.
Standardní jeřáby jsou pro nás snadné a dokážeme je vyrábět ve velkých množstvích. Přes konfigurátor si zákazník snadno zvolí parametry, které potřebuje, a pokud nemá žádné další speciální požadavky, jde zakázka přímo do systému a zadává se do výroby. Minulý rok jsme vyrobili 900 kusů těchto standardních jeřábů, ale v některých letech byla produkce i 1 400 kusů. To znamená, že na naší montážní lince dokážeme vyrábět až 8 kusů standardních jeřábů denně.
Jaký je postup výroby mostového jeřábu?
Proces můžeme rozdělit na tři hlavní celky. V první fázi se věnujeme výrobě samotného „železa“, ať už jde o profilový, krabicový anebo příhradový nosník. Podle náročnosti zakázky může tato část trvat několik hodin nebo i několik dní.
Druhá část je tryskání a lakování. Při běžných nátěrech je zde časová náročnost jeden den, aby byl povrch již suchý a schopný dalšího zpracování.
Třetí celek je montáž, kde část produktů montujeme na jednom místě a část produktů prochází montážní linkou.
Montážní linka při výrobě jeřábů? To jsem ještě neslyšel.
Práci na lince jsem zavedl už v roce 2013 ve výrobě v Německu. Po přesunu linky sem do Slaného, jsme ji v jistém smyslu dovedli k dokonalosti, ale stále nacházíme prostor k vylepšování. Naše řešení považuji v rámci koncernu za unikátní. Má 4 stanoviště: začíná se mechanickou montáží, na dalším stanovišti dojde na elektrickou montáž, na 3. stanovišti se věnujeme zkoušení a kontrole kvality a na posledním stanovišti uzavíráme balením. Zabalený jeřáb buď hned nakládáme, nebo jej zde na potřebnou dobu zaskladníme, abychom jej pak dodali na místo určení ve chvíli, kdy je vše připraveno pro montáž.
Na naší montážní lince dokážeme každých 90 minut expedovat jednu zakázku.
Dostáváme se tak k automatizaci. Jak se ve výrobě jeřábů projevují trendy Průmyslu 4.0? Robotizace, digitalizace – dají se tyto technologie u vás využít?
Průmysl 4.0 se v naší výrobě projevuje především v podpůrných systémech. Máme zde nadstavbu pro SAP, v níž si přehledně spravujeme všechny potřebné údaje o každé zakázce.
Co se týká samotné výroby, pracujeme na projektu robotického svařování, který je bohužel aktuálně utlumený kvůli problémům spojeným s pandemií nemoci covid-19. Konkrétně chceme robotizovat svařování příhradových nosníků, což by znamenalo velkou úsporu. Pokud se tato cesta osvědčí, dalším krokem bude robotické lakování.
Uvažujete o využití 3D tisku?
Využíváme 3D tisk v rámci koncernu pro některé platové komponenty. U nás se výrobě komponent nevěnujeme, ale do budoucna jsme tomu otevření.
Kam se bude ubírat další vývoj ve zdvihací technice? Například vaši příhradovou konstrukci nosníku vnímám jako přelomovou.
V konstrukci příhradového nosníku nám velmi pomohl vývoj výpočetní techniky, díky které jsme byli schopni spočítat parametry a dát materiál jen tam, kde je skutečně potřeba. Výsledkem je naše velice lehká příhradová konstrukce, na níž vlastníme řadu patentů.
Naší hlavní snahou je nabídnout zákazníkům nejen prosté zdvihání břemen, ale řešení toku materiálu, to je momentálně směr, kterým se jako koncern ubíráme.
Dovedete si v budoucnu představit průmyslovou výrobu bez jeřábů?
To se ocitáme ve sci-fi světě. Potřebovali bychom tu mít nějaké prostředky, které dokáží létat, jsou poměrně malé, a přitom mají obrovskou nosnost. To by muselo znamenat vynález antigravitačních zařízení. Potom by opravdu nastala revoluce. V takovém případě považuji za velmi pravděpodobné, že by to byla právě naše firma, která by vám podobná zařízení dodávala.
Další článek: Chránič páteře, který funguje jako „druhá kůže“, vznikl díky generativnímu designu