Obrábění složitých hliníkových komponent s nástroji Walter
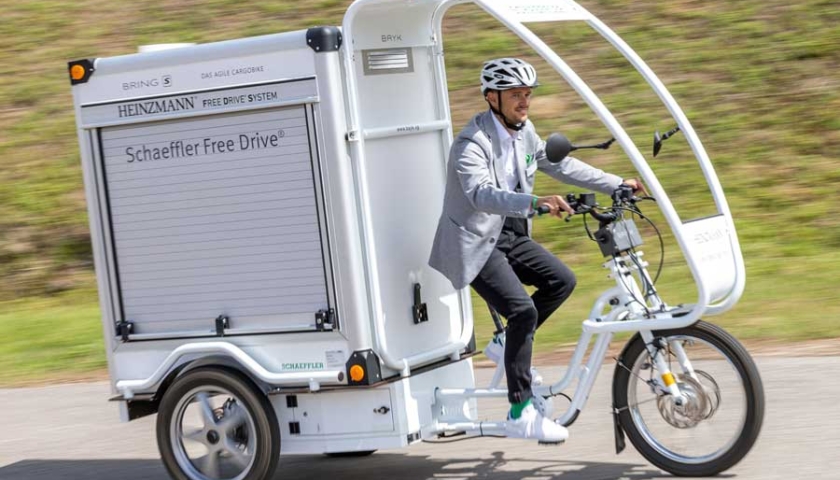
Nástup nových trendů mnohdy vyžaduje přizpůsobení výroby i souvisejícího vybavení. Vývoj speciální konstrukce nových nástrojů pro obrábění extrémně tvrdých materiálů a složitých dílů elektrokol byl úkol i pro firmu Walter. Tu ke svému novému projektu v oblasti elektromobility přizvala společnost Schaeffler.
Inzerce
Elektrokola se z nápaditého produktu stala během velmi krátké doby běžnou součástí života. Kola na bateriový pohon se stala atraktivní, uhlíkově neutrální alternativou pro kurýrní služby a logistiku na krátké vzdálenosti. S inovativním, bezřetězovým systémem Free Drive se společnost Schaeffler, která je jinak známá především jako dodavatel pro automobilový průmysl, prosazuje i v tomto sektoru. Tato inovativní technologie by se však tak rychle nemohla dostat do sériové výroby bez odborných znalostí a maximálního nasazení specialistů společnosti Walter. Ti vyvinuli vlastní konstrukci nástroje pro sériovou výrobu a implementovali ji na strojích v německém závodě společnosti Schaeffler.
Nový generátor pro pohon Free Drive
Zdá se, že elektromobilita má aktuálně problém se svojí image, a to nejen v Německu. Prodejní čísla se zkrátka nevyvíjejí podle očekávání. Jedna forma elektromobility, která však již byla přijata a otevřela mnoho dalších oblastí použití, přišla celkem rychle o svoji pozornost: elektrokola. Jízdní kola s elektrickým pohonem jsou nejen oblíbená pro volný čas, ale stávají se stále důležitější formou mobility. V některých případech už jejich nákladní a transportní verze přebírají roli dodávkových vozidel. Firmy z různých odvětví experimentují s integrací eletrokol do svých vozových parků nebo je zpřístupňují svým zaměstnancům. Elektromobilita na kole je dnes důležitou součástí snižování našich vlastních emisí CO2. Společnost Schaeffler, jako technologický lídr, se proto aktivně zapojuje do vývoje a výroby inovativních pohonných řešení i pro toto trendové odvětví.
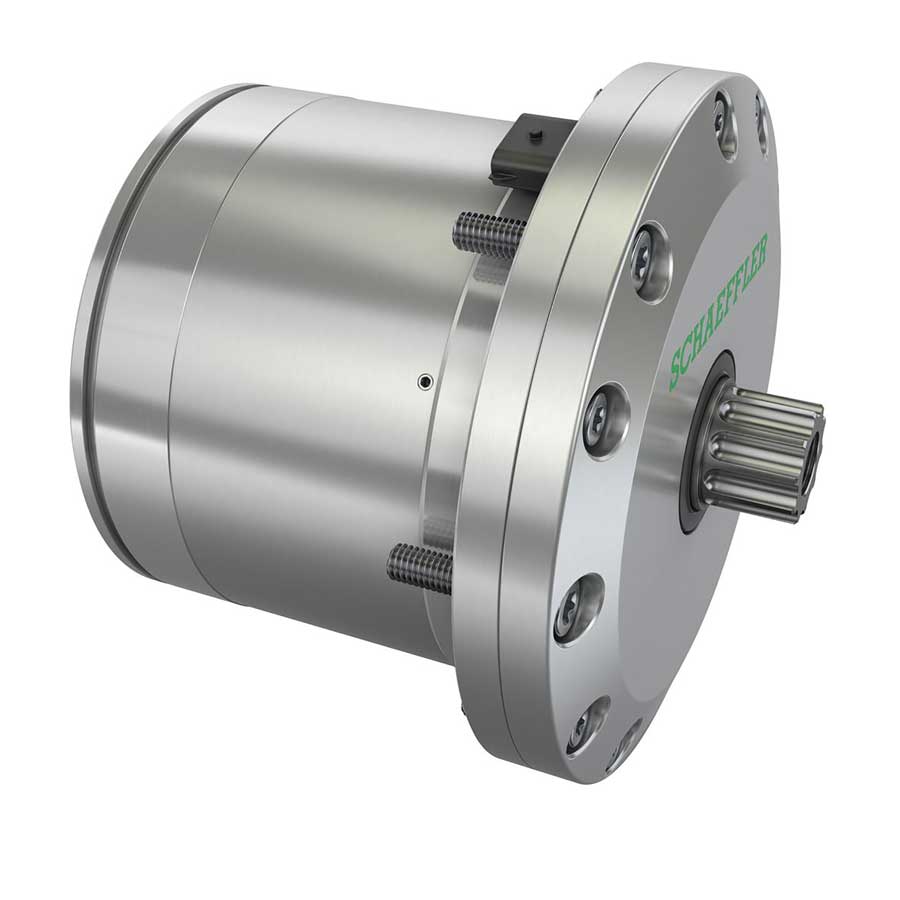
Schaeffler vyvinul inovativní pedálový generátor pro svůj bezřetězový pohon Free Drive a připravil ho pro sériovou výrobu. Jedná se o srdce systému Free Drive, který se skládá z pedálového generátoru, hnacího motoru, přizpůsobených bateriových řešení a rozhraní člověk-stroj (HMI). Pedálový generátor vytváří při šlapání konstantní odpor a dodává energii pro elektromotor na zadním kole. Jaké to přináší výhody? Při šlapání je zapotřebí mnohem méně svalové síly než u klasických řetězových pohonů, což je významná výhoda, zejména na dlouhých trasách s nákladními koly. Přebytečná energie se ukládá do baterie a v případě potřeby se využívá k pohonu. Free Drive poskytuje celkový výkon 250 wattů. Jelikož zde nejsou žádné opotřebitelné součásti, jako jsou řetězy, ozubená kola, pastorky nebo řemeny, vyžaduje systém i minimální údržbu, to je pak ideální řešení pro provoz vozových parků nákladních kol.
Složité obrábění v přísných tolerancích
Vývoj pedálového generátoru nebyl jediným technickým úspěchem. Dalším krokem bylo převedení původního návrhu komponenty do konstrukce, kterou by bylo možné nákladově efektivně a spolehlivě obrábět v závodě Schaeffler Automotive. Zvláštní pozornost je věnována krytu. Ten je frézován z pevné hliníkové slitiny, což představuje mnohé výzvy. Například na dně 85milimetrového hlubokého krytu musí být frézovány profily a drážky. Kryt je navíc velmi tenkostěnný, což ztěžuje dodržení přísných tolerancí kruhovitosti během obrábění.
Obrábění hliníkových komponent není pro společnost Schaeffler žádnou novinkou, avšak skutečnost, že se jedná o komponenty pro elektrolokolo, je změna. Zaměstnanci zde obvykle pracují na komponentách pro automobily se spalovacími nebo elektrickými motory, včetně tlumičů, elektrických náprav, měničů točivého momentu a dvojitých spojek. Každý den je zde na téměř devadesáti obráběcích strojích zpracováno přibližně 150 tun surového materiálu do 100 000 jednotlivých kusů.

Stefan Oberle, vedoucí technologie obrábění ve společnosti Schaeffler v Bühlu a Sasbachu, říká: „Důležitým faktorem umožňujícím hromadnou výrobu pedálového generátoru Free Drive bylo vytvoření konceptu obrábění a nástrojů, který by nás udržel v určitém nákladovém rámci. Se společností Walter jsme si mohli být jisti, že jí úkol jednoduše předáme a dostaneme skutečně dobrý výsledek.“ Mathias Scherer, specialista Walter FSE, který se o společnost Schaeffler stará již mnoho let, pak dodává: „Walter má mnoho zkušeností s projekty obrábění hliníku pro elektromobilitu a komponenty pro elektrokola jsou na vzestupu. Ve svém volném čase jsem nadšeným jezdcem na horském elektrokole, a proto jsem obzvlášť hrdý na to, že nám Schaeffler tuto práci svěřil. Mohli jsme zde plně využít naše zkušenosti – i naše široké portfolio nástrojů a služeb.“
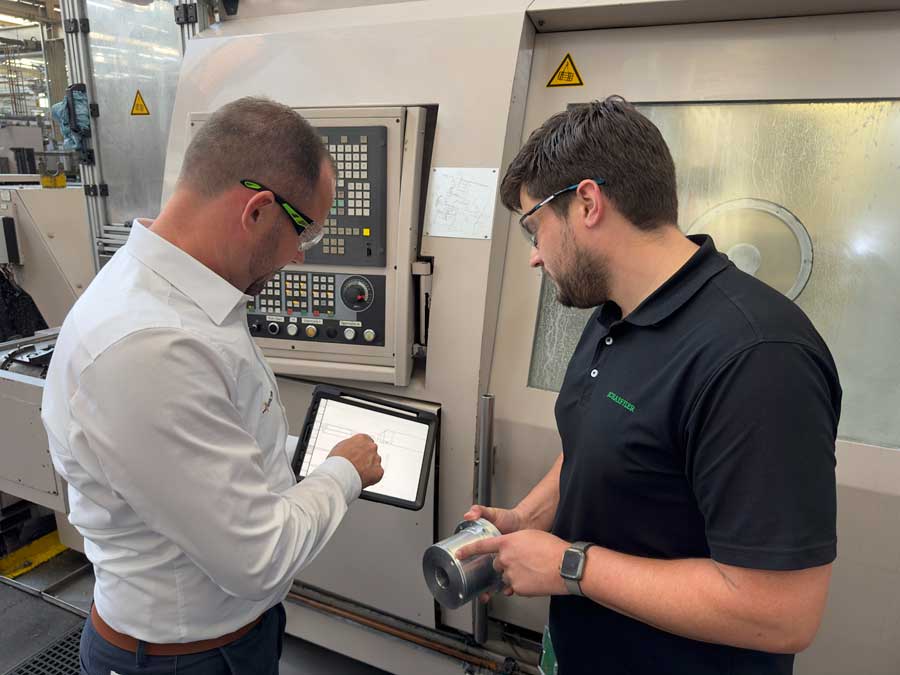
Návrh nástrojů pod taktovkou Walter
Pro obrábění krytu a víka generátoru se v současném nastavení používá celkem 25 obráběcích nástrojů, včetně MD266, rohové/drážkovací frézy ze slinutého karbidu. Návrh je výsledkem úzké spolupráce mezi společnostmi Walter a Schaeffler. Michael Benz, aplikační inženýr ve společnosti Walter, byl součástí projektu od samého začátku: „Základní rámec pro návrh nástrojů byl stanoven poměrně rychle. Ale teprve na stroji se ukáže, co skutečně funguje dobře. Ve společnosti Walter můžeme čerpat z velmi různorodého portfolia nástrojů k optimalizaci procesu. Co však často tvoří zásadní rozdíl, jsou v případě aplikačních techniků firmy Walter vlastní zkušenosti s obráběním.“ Stefan Oberle pak vidí tuto odbornou praxi jako jednu ze silných stránek společnosti Walter: „Spolupracujeme s velkým počtem výrobců nástrojů. Technická odbornost a praktické zkušenosti týmu Walter v oblasti obrábění jsou zřejmé na první pohled, což je u složitých projektů vždy velkou výhodou, zejména když je důležitá i strategie obrábění,“ uzavřel spokojeně Oberle.
Díky další vydařené spolupráci a vhodně navrženému řešení si tak Walter opět upevnil pozici spolehlivého dodavatele nástrojů a obráběcích technologií napříč průmyslovými obory.
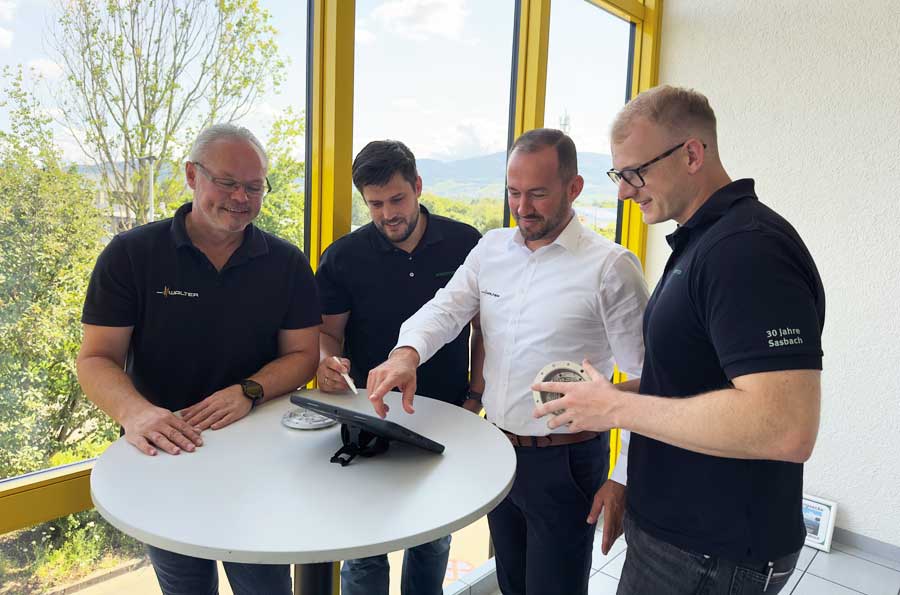