Spolehlivé svařování venkovního střídače odolného vůči povětrnosti
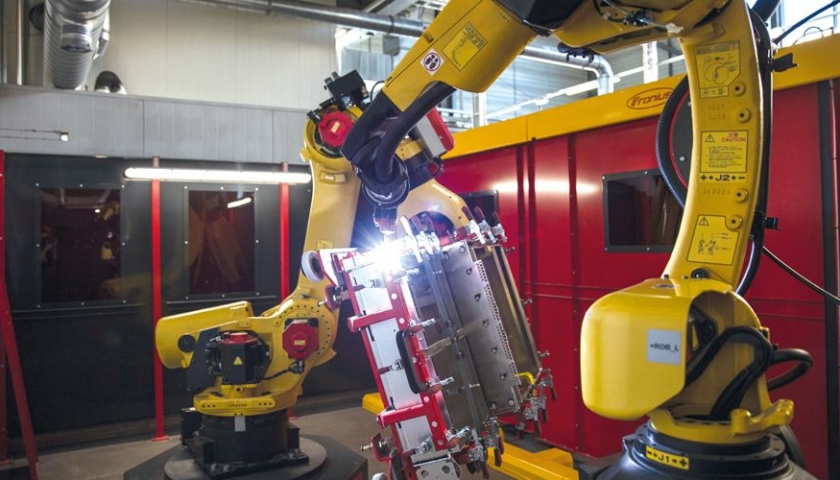
Společnost Fronius Solar Energy v Rakousku je od samého počátku průkopníkem v oblasti solární energie. Příběh začíná v roce 1992 a rychle nabírá na obrátkách.
Inzerce
Brzy po začátku je na trh uveden první střídač Fronius Sunrise. Od té doby následují stále nová fotovoltaická řešení a inovace. Vizí solárních nadšenců je „24 hodin slunce“, svět, ve kterém 100 procent energie pochází z obnovitelných zdrojů. Nejnovější střídač se jmenuje Tauro. Je neprodyšně svařený po celém obvodu pomocí nejnovější generace robotického svařovacího systému Handling-to-Welding a určený pro komerční venkovní použití, takže odolá každému počasí.
Dvoustěnný, aktivně chlazený plášť umožňuje používat střídač Tauro venku. Nezáleží na tom, zda prší, je horko, nebo svítí přímé slunce – střídač to ustojí a odvede svou práci na 100 procent. Je navržen pokrokovými odborníky na solární energii a splňuje mezinárodní stupeň krytí IP65. Špičková technologická zařízení tohoto druhu jsou chráněna proti dotyku, vodě tryskající z kteréhokoliv úhlu a vniknutí prachu. „Svařování hliníkových plášťů je vzhledem k různým tloušťkám plechů velmi náročné,“ vysvětluje Jasmin Gross, Fronius Solar Energy. „Ve společnosti Fronius Welding Automation máme dokonalého partnera pod vlastní střechou.“
Nejprve se simuluje
Střídač se vyrábí v rakouském Sattledtu. Plášť a křídlová dvířka se svařují v nejmodernější robotické svařovací buňce „Handling-to-Welding“ speciálně vyvinuté pro tento úkol. „Všechny pohyby robota a pořadí svarů programujeme a simulujeme offline pomocí programu Fronius Pathfinder, tj. odděleně od systému na digitálním dvojčeti,“ vysvětluje Anton Leithenmair, vedoucí Welding Automation. „Díky tomu můžeme předem odhalit případné rušivé obrysy. Totéž platí pro limity os a nastavení hořáků. I zde dokážeme zasáhnout včas, ne až při prvních svařovacích zkouškách. Po naprogramování pořadí svarů předá Pathfinder data postprocesoru, který je přeloží do jazyka robotů Fanuc. Tímto způsobem šetříme drahocenný čas a náklady. Offline programování zkrátí výuku robota ve svařovací buňce o mnoho hodin!“
Plánování pracovních postupů minutu po minutě
Před zahájením výroby se v systému plánování podnikových zdrojů (ERP) vytvoří prodejní objednávky střídače Tauro, které tvoří základ pro tzv. běh Manufacturing Resource Planning (běh MRP). Zde se vytvářejí všechny výrobní objednávky plášťů a křídlových dvířek. Dále se každé objednávce přiřadí datum výroby. Následné podrobné plánování provádí systém MES (Manufacturing Execution System). Každá objednávka se naplánuje na minutu přesně, přiřadí se k volnému koridoru objednávek a poté se zařadí do seznamu.
Dokonalý soulad: stehování, příprava, svařování
Svařování dvoustěnných plášťů střídačů je vzhledem k rozdílným tloušťkám plechů od samého počátku velmi náročné. „Dříve než jednotlivé plechové prvky standardně spojíme v robotické svařovací buňce, ručně je sestehujeme. K tomu používáme proces MAG. Už tady se musí precizně pracovat,“ tvrdí Christian Kraus, skupinový vedoucí ve výrobně plechů.
Jakmile je stehování dokončené a zaevidované na terminálu systému, centrální systémové řízení uvolní další pracovní krok – robotizované svařování. Nyní se plášť položí a upne na technický vozík a vjede do propusti. Po příslušném potvrzení systém spustí další úlohu a pomocí čipu RFID (Radio Frequency Identification) se na upínacím zařízení vybere program robota odpovědný za polohování a svařování.
„Nezáleží na tom, který díl do propusti vložíme: Čip RFID ví, který svařovací program se použije,“ doplňuje Kraus. „Můžeme například obsadit první propust pláštěm střídače, zatímco díky podavači dílů ve druhé propusti svařujeme křídlová dvířka. A naopak. Použití technologie RFID nám dává možnost svařovat díly zcela nezávisle na tvaru, velikosti a množství. Naše robotická svařovací buňka Handling-to-Welding zvládne velikost dávky 1 stejně jako sériovou výrobu.“
Robotika a svařovací technologie z nejvybranějších
Po spuštění svařovacího procesu manipulační robot Fanuc R-2000iD/210FH uchopí díl a dopraví ho do svařovací buňky. Plášť střídače je pro něj celkem lehká váha. S dosahem 2,6 metru je nosnost 210 kilogramů, přičemž hliníkový plášť včetně upínacího zařízení váží maximálně 140 kilogramů. Po dopravení pláště střídače Tauro do svařovací buňky se na dno pláště pomocí inkoustové technologie vytiskne datový maticový kód (DMC). Tento kód obsahuje sériová čísla jednotlivých plášťů střídače Tauro, která jsou propojená se svařovacími daty zaznamenanými během svařovacího procesu softwarem pro správu dat WeldCube. Takže na konci je každý jednotlivý svar stoprocentně vysledovatelný.
Po natištění DMC začíná vlastní svařovací proces. Zatímco svařovací robot Fanuc ARC Mate 100iD odvádí svou práci a spojuje 5,5 metru hliníkového plechu celkem 96 svary, manipulační robot přenáší plášť do ideální polohy. Některé svary vyžadují dokonalé simultánní pohyby obou robotů, což je vysoké umění robotizovaného svařování.
„Jako svařovací proces se používá převážně Pulse Multi Control Ripple Drive“, dále vysvětluje pan Leithenmair. „PMC Ripple Drive umožňuje přesné nastavení vnosu tepla a dokonale se hodí pro spojování různě silných plechů.“
Krásně šupinaté svary
Přesněji řečeno, PMC Ripple Drive je zvláštním typem procesu PMC. Vyznačuje se cyklickým střídáním procesu PMC a vratným pohybem drátu pomocí takzvané hnací jednotky PushPull. Svařování metodou PMC je ideální pro automatizované svařování a je mnohem rychlejší než svařování metodou TIG. Přitom tento proces poskytuje stejné, krásně šupinaté a téměř bezrozstřikové svary.
Jako přídavný materiál se používá hliníkovo-křemíkový drát o tloušťce 1,2 mm, který se svařuje pod ochranným plynem argonem. Svařovací procesy, dráty a plyny jsou zahrnuty v systémových informacích k svařovací úloze.
Po dokončení 17,5minutového svařovacího cyklu umístí manipulační robot díl do propusti a svařovací buňka vyšle signál o dokončení do systému MES. Zatímco se jedna propust vyprazdňuje, ve druhé už může začít další práce.
Vše pod kontrolou – prediktivní údržba
Systém MES (Manufacturing Execution System) spravuje velké množství dat. Kromě správy objednávek se zaznamenávají také stavy stroje, doby taktu, poruchy a hodnoty vakuové zkoušky, která se provádí na konci celého svařovacího procesu. Pomocí systému MES lze také definovat okna údržby. Pokud se například ukáže, že k určité poruše dochází v průměru každých 100 provozních hodin, lze nastavit cílový interval údržby na 99 hodin. Systematicky plánované údržbářské práce v předstihu prodlužují životnost svařovacího zdroje a zabraňují zbytečným prostojům.
Krytí IP65 předpokládá dokonalé svary
Několik detailů pláště, které jsou mimo optimální dosah robota, se svaří ručně. Zde se používá proces TIG, který je předurčený pro svařování hliníku. Na konci svařování se obrousí všechna případná převýšení svaru, svary se natřou penetračním barvivem a zkontrolují se, zda neobsahují vady. Zkušební kapalina přitom proniká všemi nepravidelnostmi materiálu.
Po zkoušce svarových švů putuje každý plášť bez závad do zařízení pro kontrolu těsnosti, které společnost Fronius vyvinula speciálně pro Tauro. Uvnitř pláště střídače se vytvoří podtlak 60 milibarů, který musí vydržet po přesně stanovenou dobu. Pokud během této doby poklesne tlak o méně než 1,8 milibarů, je kryt stoprocentně těsný a splňuje stupeň krytí IP65.
Po úspěšném dokončení zkoušky těsnosti se výsledek uloží do systému WeldCube podle sériového čísla a je zaručena kompletní vysledovatelnost. Plášť střídače je nyní připraven k následnému práškovému lakování. Na konci výrobního řetězce, po sestavení, stojí střídač pro velké systémy, který odolá všem povětrnostním podmínkám.
Další článek: UV záření a vlhko: Energetické řetězy v experimentálním projektu